3D Printing First Layer:
Problems & Solutions
3D Printing First Layer:
Problems & Solutions
Guide to Troubleshooting 3D Printing First Layer Problems
3D printing first layer is more than just another part of the process – it’s the foundation of everything that is printed after. A well-printed first layer ensures good adhesion to the build plate and minimizes issues such as warping or failed prints, while a poorly-constructed first layer accelerates these problems. Discover possible solutions to significantly reduce your 3D printing first layer problems.
Understanding the First Layer
The first layer is crucial in photopolymer-based 3D printing such as Stereolithography (SLA) or Digital Light Processing (DLP). In these processes, the first layer must adhere strongly to the build plate to prevent detachment during the print.
The first layer typically receives extra exposure time to ensure it bonds securely to the build plate and to create a stable base for the rest of the print.
Achieving a good first layer requires several factors:
- The build plate must be precisely levelled to ensure even resin distribution.
- Photopolymers require precise light exposure to solidify effectively.
- An extended exposure time is often used for the initial layers to enhance adhesion to the build plate.
If the first layer does not adhere properly, issues such as warping, detachment, or failed prints may occur.
Common 3D Printing First Layer Problems
Whether we talk about 3D printing in dentistry, automotive or wearable technology, 3D printing first layer issues remain a common challenge, ranging from adhesion problems to warping or lifting edges.
The following sections present the most common problems as well as possible solutions.
Poor Adhesion to the Build Plate
- Problem: The first layer does not stick properly, leading to print failures or detachment.
- Solution: Ensure the build plate is levelled correctly, increase the bottom layer exposure time, and clean the plate thoroughly. A slight increase in Z-offset may also help.
When the first layer does not adhere properly, prints may detach mid-process or fail entirely. This issue is often caused by an unlevelled build plate, insufficient exposure time, or contamination on the plate.
Over-Adhesion to the Build Plate
- Problem: The print sticks too well, making removal difficult and risking damage.
- Solution: Reduce the bottom layer exposure time slightly or use a flexible or textured build plate for easier removal.
Finding the right adhesion to the build plate often equals a balance act. While you need to avoid poor adhesion of a print to the build plate, sticking too firmly makes the removal challenging, which could lead to damage.
Uneven First Layer
- Problem: The first layer appears distorted, inconsistent, or uneven.
- Solution: Check for a properly levelled build plate, ensure the vat is free of cured resin debris, and verify uniform resin distribution before printing.
An uneven first layer can cause print defects, which lead to failed prints or poor surface quality. This issue may arise from an improperly levelled build plate, trapped cured resin particles in the vat, or uneven resin distribution.
Thin or Weak First Layer
- Problem: The first layer is too thin or fragile, leading to weak adhesion and layer separation.
- Solution: Increase the number of bottom layers and slightly adjust the bottom exposure time for better layer bonding.
A first layer that appears too thin or fragile may lead to layer separation and adhesion failures. This problem usually results from an inadequate number of bottom layers, incorrect exposure settings, or an imbalanced Z-offset.
Warping or Lifting Edges
- Problem: The edges of the first layer peel up or warp.
- Solution: Increase bottom layer exposure time, ensure a clean build plate, and avoid printing in a cold environment, as temperature fluctuations can affect adhesion.
Peeling or warping occurs when the first layer curls up or separates from the build plate. This problem is often due to insufficient bottom layer exposure, an unclean build plate, or environmental factors such as temperature fluctuations.
Optimizing First Layer Success
While 3D printing first layer problems can be manifold, there are quite a few steps you can take to diminish the problems and increase your success rate significantly.
- Ensure a clean build plate: Always clean the build plate with isopropyl alcohol to remove dust, oils, or cured resin residue.
- Platform levelling: If adhesion remains weak, slightly decrease the Z-offset or use a build plate with a textured surface to improve bonding between the resin and the plate, or adjust the Z-offset slightly higher in case of excessive adhesion.
- Control lift speed: The first-layer lift speed should usually be lower than standard lift speeds to reduce suction forces and ensure proper separation from the FEP film.
- Exposure time: Adjust the first-layer exposure time, as insufficient curing can cause adhesion failures, while excessive exposure may lead to over-adhesion.
- Stable temperatures: Maintain a stable printing environment to prevent warping. Most photopolymer resins work best between 24–30 °C (75–86 °F).
- FEP film quality: At last, regularly check and replace the FEP film when worn or scratched in order to prevent adhesion issues and to maintain a consistent print quality.
RAHN: Your Reliable Material Supplier
3D printing first layer problems require a precise approach to material selection and printing conditions. RAHN is your 3D printing solutions provider and reliable supply partner. Contact us to find out more about reliable printing solutions for a wide range of applications and industries.
Your personal contact
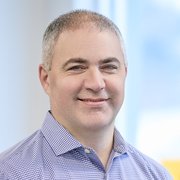
Christopher Cocklan
3D Printing Business Development Manager EnergyCuring
RAHN USA Corp.