3D Printing
Photopolymer Composites
3D Printing
Photopolymer Composites
3D Printing Photopolymer Composites: Properties and Applications
When it comes to 3D printing, the choice of the right materials is crucial to create a product with specific properties. This is where polymer composites come into play.
3D printing of polymer composites offers the flexibility to create products with custom properties, such as reduced shrinkage and improved durability.
What Are Photopolymer Composites?
To better understand what 3D printing of polymer composites entails, it is worthwhile to take a look at the definition. The term “photopolymer composites” is made up of 2 distinct definitions:
- Photopolymer: A photopolymer is any material that changes its physical or chemical properties when exposed to light.
- Composites: A composite material is formed by combining two substances with varying physical and chemical characteristics. They are customised for specific functions, such as increased strength, reduced weight, or enhanced electrical resistance. Typically, composites comprise only two components: the matrix or binder, which encases and amalgamates fibres or fragments of the other material, which is known as the reinforcement.
Bringing these terms together, photopolymer composites are a particular kind of composite material, in which a photopolymer acts as the central matrix element. The photopolymer is mixed with a reinforcing phase, which can be made up of fibres, particles, or other materials. When subjected to the right light source, the photopolymer matrix undergoes photopolymerisation, resulting in the material becoming solidified.
Reinforcement Materials Used in Photopolymer Composites
The used reinforcement material is crucial to create 3D printing composites with specific characteristics. Common reinforcement materials include carbon fibres, glass fibres, aramid fibres, and nanoparticles.
Carbon Fibres
Carbon fibre reinforced polymers are composite materials where the strength and rigidity are primarily derived from the carbon fibre, while the polymer acts as a binding matrix, safeguarding and uniting the fibres, while contributing some degree of resilience. Carbon fibre-reinforced polymers are now widely employed in situations demanding exceptional mechanical characteristics alongside weight reduction, such as the Airbus A350 XWB or the Boeing 787 Dreamliner, both of which incorporate fibre composites in approximately 50% of their wings, fuselage sections, and tail surfaces
Glass Fibres
Glass fibres offer multiple advantages for a wide range of applications. While the stiffness of glass fibre is comparatively lower than some other reinforcing fibres, it offers the significant advantage of combining a high strength with a low density. Further, the costs are relatively low. They are used in aerospace for components like aircraft interiors and structural elements. In the automotive industry, these composites are employed for parts that require high strength-to-weight ratios, such as body panels and interior components. Additionally, they are used in consumer goods like sporting equipment and electronics casings. The medical field also benefits from these composites in applications like prosthetics and dental devices.
Aramid Fibres
As a fibre-reinforced polymer (FRP), aramid fibres, like carbon and glass fibres, have unique self-lubricating capabilities. They are also known for their good mechanical properties, such as density, high tenacity, and high impact resistance. Aramid fibres, such as Kevlar, are known for their exceptional strength-to-weight ratio, surpassing that of glass fibres. They also exhibit higher impact resistance, making them suitable for applications where durability is critical. Additionally, aramid fibres have excellent resistance to chemicals and abrasion. They are an ideal insulator of heat and electricity and are resistant to organic solvents, fuels, and lubricants.
Nanoparticles
A nanoparticle measures between 1 and 100 nanometres. Invisible to the eye, nanoparticles can display distinct physical and chemical properties compared to their larger counterparts. Composites made of nanoparticles are engineered to have enhanced attributes, such as improved strength, conductivity, or other specialised characteristics. They find applications in various industries, including electronics, aerospace, and biomedical fields, where control over material properties at the nanoscale is crucial.
Advantages of Photopolymer Composites
By incorporating additional materials, photopolymer composites can exhibit enhanced mechanical properties, such as increased strength, stiffness, and impact resistance. They can also be engineered to possess specific characteristics like conductivity or flame resistance, which may not be achievable with pure photopolymers alone. Moreover, incorporating Vat photopolymerization techniques within photopolymer composites offers an additional advantage by enabling precise control over the curing process, resulting in enhanced uniformity and structural integrity of printed parts.
Enhanced Mechanical Properties
Photopolymer composites offer distinct advantages over pure photopolymers, particularly in terms of enhanced mechanical properties. By incorporating additional materials, these composites can achieve heightened levels of strength, rigidity, and durability. This improvement in mechanical attributes makes them highly desirable for applications where structural integrity and performance are paramount, such as in aerospace components or automotive parts. The integration of supplementary materials enables photopolymer composites to surpass the mechanical capabilities of their pure photopolymer counterparts.
Versatile Usage
By incorporating additional materials, photopolymer composites can be adjusted to exhibit virtually every desired characteristic. The versatility of photopolymer composites is essential for applications that demand precise material properties. For instance, UV and thermal stability as well as chemical resistance enables the final product to withstand external exposures, while low outgassing properties are needed in the aerospace industry to release minimal volatile substances when subjected to vacuum conditions. Therefore, 3D printing composites is everything needed to create a product suitable for innumerable applications.
Customizable Properties
3D printing of polymer composites can be finely tuned to exhibit specific characteristics such as conductivity, flame resistance, or enhanced thermal stability. This level of customisation allows for tailored solutions in various industries. The versatility of photopolymer composites is an invaluable choice for applications that demand specialised material properties.
Reduced Shrinkage
When choosing the right components, reduced shrinkage is essential for applications, in which dimensional accuracy is crucial. The customizability of photopolymer composites, with a focus on minimising shrinkage, makes 3D printing composites a preferred choice for industries that demand meticulous precision in their final products.
Improved Dimensional Stability
Dimensional stability refers to a material's ability to maintain its original shape and size when subjected to various external factors, such as temperature changes, humidity, or mechanical stress. This characteristic is highly beneficial in applications where precise and accurate dimensions are crucial.
Improved Resistance
Photopolymer composites can exhibit greater durability and resilience to various external factors, such as mechanical stress, chemicals, or environmental conditions. This enhanced resistance makes them well-suited for applications where robustness and longevity are critical, such as in aerospace components, automotive parts, and industrial machinery. In essence, the heightened resistance of photopolymer composites sets them apart as a superior choice in situations demanding exceptional durability and performance.
Applications of 3D Printing With Photopolymer Composites
3D printing of polymer composites finds diverse applications across several industries due to its unique capabilities. It allows for rapid prototyping and iterative designs, enabling engineers and designers to quickly test concepts. Beyond industries like aerospace and healthcare, 3D printing in construction is also gaining traction, offering new possibilities for durable, lightweight, and sustainable building materials.
In aerospace, photopolymer composites are utilised to manufacture lightweight yet robust components, such as interior fittings, brackets, and prototypes for aerodynamic testing, while the automotive industry uses the materials for interior trim, custom fixtures, and prototypes for vehicle testing, just to name a few.
The medical field benefits from 3D printing composites for creating intricate anatomical models for surgical planning, as well as patient-specific implants. Dentistry employs this technology for crafting dental crowns, bridges, and models for prosthodontics.
Even the jewellery industry makes use of photopolymer composites for producing intricate and custom-designed jewellery pieces with fine details. The applications of 3D printing with photopolymer composites are vast and continue to expand as technology advances, offering versatile solutions across a wide array of industries.
Photopolymer Composites – A Fully Bespoke And Reliable Solution
The ability to be tailored to specific needs coupled with their reliability makes photopolymer composites a cornerstone in 3D printing. Whether in aerospace, healthcare, or jewellery, photopolymer composites continue to pave the way for innovative and precise solutions in diverse industries.
Contact us to find out more about our 3D printing solutions and about how photopolymer composites enhance your processes.
Your personal contact
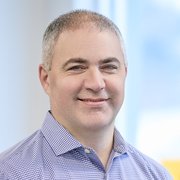
Christopher Cocklan
3D Printing Business Development Manager EnergyCuring
RAHN USA Corp.