A guide to
SLA 3D printing
A guide to
SLA 3D printing
A guide to SLA 3D Printing
SLA is an acronym for Stereolithography, which is a method of 3D printing. It is one of the oldest types of 3D printing. This method can be used to produce parts for both prototyping and functional use with a wide range of utilities and properties.
While there can be several different types of SLA 3D printing the common theme is that a laser or light source irradiates specific patterns on a photosensitive resin one very thin layer at a time until an object is fully formed. This method has the ability to produce extremely fine and accurate details which allows it to be used in a vast variety of applications.
1. Understanding SLA 3D Printing Technology
Stereolithography (SLA) is one of the most widely used 3D printing technologies, known for producing highly detailed, smooth, and accurate parts. It operates by curing liquid photopolymers into solid objects layer by layer using an ultraviolet (UV) laser. Unlike other methods like FDM, which extrudes filament, SLA focuses on precision and is commonly used for prototypes, molds, and highly intricate designs.
Common Forms of SLA 3D Printing
SLA 3D printing typically is available in two versions: top-down and bottom-up. In top down arrangement, the print base is submerged below the liquid resin surface and after each layer is irradiated the base drops down a tiny fraction so that the next layer can be created. The resolution of the prints are determined by the width of the laser which explains why the detail is so good. There are some drawbacks with this method in that you typically need to use more resin volume than other photopolymer methods, and the time can be a bit longer due to the laser having to trace every layer. For applications that require even finer detail, microstereolithography (MSL) takes SLA technology to the next level. MSL offers unmatched precision, enabling the creation of highly intricate microstructures that are difficult to achieve with traditional SLA
In bottom-up situations of SLA 3D printing, the laser is situated below a vat of photopolymer and shines through a film, or window. The build plate is held a very specific distance above the film, submerged in the resin. After each layer is irradiated, the base pulls away from the film to allow liquid resin to flow back over the window and the base is then returned, this time leaving the same gap between the window and the last layer printed.
This method has benefits in that you tend to be able to use much less resin for a given build volume. Printers and parts also tend to be less expensive. The main drawbacks are that there tend to be smaller build areas available, and there is more service/troubleshooting required.
A newer version of SLA 3D printing is called mSLA or "masked" SLA. This can also be called LCD printing whereby a single light source (not a laser) is used, and an LCD screen is used to mask where irradiation is not desired. Virtually all of the other operations/mechanics are the same. One major benefit is lower cost as the light source is much less expensive, but it also tends to be faster.
2. Key Considerations for Choosing SLA 3D Printing Materials
When choosing SLA 3D printing materials, several factors must be taken into account to ensure the material fits the project’s needs. Important considerations include:
- Material Properties: Different resins offer varying levels of strength, flexibility, and heat resistance. For instance, engineering resins can mimic ABS or polypropylene properties, while flexible resins are suited for soft-touch components.
- Application Requirements: The choice of material should align with the end-use of the part. If you're creating prototypes, a standard resin may suffice, but for functional parts, you might need durable, heat-resistant, or biocompatible resins.
- Surface Finish and Detail: SLA excels in creating parts with high detail and smooth finishes. However, some resins are better suited for this than others, particularly if your project requires extreme precision or fine features.
- Post-Processing Needs: Consider how much post-processing is required. Some SLA resins may need additional UV curing, sanding, or painting to achieve the desired finish.
By understanding these considerations, you can select the optimal material for your specific SLA 3D printing project, ensuring both performance and quality
Requirements for SLA 3D printing materials
Requirements of 3D printing resins for these methods tend to be relatively similar. Lower viscosity is better as it allows for fast and uniform recoating/refilling. Low shrinkage allows for little to no warping (which is especially important for fine details and larger structures. One aspect that needs to be considered in bottom-up printers is compatibility with the window material.
You do not want SLA 3D printing materials that will swell, cloud, or otherwise attack the window material (typically either PDMS or FEP). You obviously do not want anything to adhere to the window after curing as that can lead to delamination of layers, or other destruction of the print.
Overview of SLA 3D Printing Materials
SLA 3D printing offers a variety of material options, each tailored to different applications, from prototypes to functional parts. These resins vary in terms of flexibility, durability, heat resistance, and more, allowing SLA to serve a wide range of industries. Choosing the right resin depends on the specific needs of your project, such as surface finish, strength, or biocompatibility. Whether you're creating aesthetic prototypes or functional components, the wide selection of SLA materials ensures there’s a suitable option for your goals.
Material Properties and Their Impact on Printing
The properties of SLA materials play a crucial role in the final quality and functionality of the printed parts. Different resins offer various degrees of toughness, flexibility, and heat resistance. For example, engineering resins provide strong, impact-resistant parts, while flexible resins enable the production of soft, pliable components. The choice of material impacts not only the physical properties of the printed parts but also how well they meet performance criteria such as durability, precision, or thermal stability. Selecting the right material ensures the best results for the intended use.
3. Exploring SLA 3D Printing Materials
SLA 3D printing offers a diverse range of materials that cater to various applications, from basic prototyping to highly specialized industrial and medical uses. Understanding the capabilities of these resins can help you select the right material for your project, ensuring optimal performance, precision, and durability. Below, we explore some of the most commonly used SLA 3D printing materials.
Standard Resins
Standard resins are ideal for rapid prototyping and visual models. These resins are known for producing parts with smooth surfaces and high detail, making them perfect for creating presentation models or fit-checking prototypes. While they offer good aesthetics, they are generally less durable than engineering-grade resins and may become brittle over time. Standard resins are best suited for projects where appearance and surface finish are prioritized over mechanical strength.
Engineering Resins
Engineering resins are designed to mimic the mechanical properties of industrial plastics like ABS, polypropylene, and nylon. These resins are used for functional parts that require durability, toughness, and impact resistance. Engineering resins excel in applications where mechanical strength and thermal stability are critical, such as creating end-use parts, functional prototypes, and components for mechanical assemblies. They are often chosen for testing parts under real-world conditions or for producing limited-run, high-performance components.
Medical and Dental Resins
SLA 3D printing has revolutionized the medical and dental fields by providing highly accurate, biocompatible materials suitable for direct contact with the human body. Medical and dental resins meet strict regulatory standards for biocompatibility and are used in applications such as surgical guides, dental models, clear aligners, and custom implants. These resins offer precise detail and smooth surfaces, which are essential for creating patient-specific devices and models that need to fit perfectly.
Flexible and Tough Resins
Flexible and tough resins offer distinct advantages for parts that require flexibility or the ability to withstand high mechanical stress. Flexible resins can create soft, bendable parts ideal for 3D-printed wearables, gaskets, or ergonomic components. They provide excellent elongation and durability, making them suitable for dynamic applications. Tough resins, on the other hand, are formulated to absorb impact and resist breaking under stress. These resins are often used in functional prototypes, snap-fit assemblies, and rugged components where resilience is crucial.
4. Applications of SLA 3D Printing Materials
Thanks to its unmatched accuracy and precision, and broad choice of materials, SLA 3D Printing is a very versatile, and an effective means to produce both prototypes and production pieces.
It’s utilized across various sectors including 3D printing in dentistry and industries like manufacturing and engineering, with its applications extending to the expansive field of 3D printing in healthcare.
Prototyping
One of the most common uses of SLA 3D printing is in prototyping, where its ability to produce highly accurate and detailed models is invaluable. Companies across industries use SLA for creating early-stage designs and prototypes that closely mimic the final product. Standard resins are typically used in this application due to their balance of cost and precision. Whether for visual models, fit testing, or concept verification, SLA enables fast, high-quality prototyping that helps speed up the product development cycle.
Functional Parts
SLA 3D printing materials, especially engineering and tough resins, are ideal for creating functional parts that need to withstand mechanical stress or environmental factors. These resins mimic the properties of industrial plastics like ABS or polypropylene, making them suitable for end-use components or functional testing. From snap-fit assemblies to custom tooling, SLA 3D printing provides the strength and durability required for demanding applications. Additionally, high-temperature resins are used for parts that will be exposed to elevated temperatures, such as molds or automotive components.
Artistic and Jewelry Applications
The precision and smooth surface finish of SLA make it an excellent choice for artistic applications, including jewelry making. Artists and jewelers use SLA to create intricate, highly detailed pieces that would be difficult or impossible to achieve with traditional manufacturing methods. SLA enables the creation of complex designs with fine details, perfect for custom jewelry, sculptures, and small art pieces. Flexible resins and clear materials are often used to craft unique, artistic products that require both visual appeal and functional flexibility.
5. Advantages and Challenges of SLA 3D Printing
SLA 3D printing offers many benefits that make it a popular choice in industries requiring high precision and smooth surface finishes. However, like any technology, it comes with its own set of challenges. Understanding the pros and cons of SLA can help you decide whether it’s the right solution for your specific needs.
Benefits of SLA 3D Printing
High Precision and Detail: SLA is known for producing parts with exceptional accuracy, making it ideal for prototypes, models, and parts that require fine details. The technology allows for intricate geometries and smooth surfaces that would be difficult to achieve with other 3D printing methods.
Smooth Surface Finish: SLA parts often require minimal post-processing, as the technology produces smooth surfaces directly from the print. This is particularly useful for applications where aesthetics or surface finish quality are important, such as in consumer products or artistic applications.
Versatility of Materials: SLA offers a broad range of resins, from standard resins to highly specialized ones like tough, flexible, biocompatible, and high-temperature resins. This versatility makes it suitable for a wide range of applications, including prototyping, functional parts, medical models, and artistic creations
Fast Prototyping: SLA enables quick turnaround times for prototypes, reducing the time needed for product development. Its ability to create precise and functional models allows designers to test and refine their ideas faster than traditional manufacturing methods.
Ideal for Small, Detailed Parts: SLA excels at creating small, detailed parts that require a high degree of accuracy. This makes it particularly valuable in industries like jewelry, dental, and medical device manufacturing, where precision is essential
Challenges and Considerations
Material Limitations: While SLA resins offer a wide variety of options, they are typically more brittle than other 3D printing materials like those used in FDM or SLS. SLA parts may not be suitable for high-impact or load-bearing applications unless specialized resins are used.
Post-Processing Requirements: Although SLA prints have a smooth surface, they often require post-processing steps such as washing and additional UV curing to fully harden the material. This adds extra time to the production process and can increase the overall cost.
Cost of Materials and Equipment: SLA printers and resins tend to be more expensive compared to other 3D printing technologies like FDM. The high-quality finish and precision come at a premium, making SLA more costly, particularly for larger production runs.
Fragility of Parts: Depending on the resin used, SLA parts can be fragile and prone to cracking or breaking under stress. While some resins offer enhanced toughness, SLA is generally better suited for applications where strength is less critical.
Build Size Constraints: SLA machines typically have smaller build volumes than other 3D printing technologies like FDM or SLS. This limits the size of the parts that can be printed in one go, requiring larger objects to be printed in multiple pieces and assembled later.
By weighing these advantages and challenges, you can determine whether SLA is the best choice for your specific 3D printing needs.
Future Trends in SLA 3D Printing Materials
As the demand for more advanced and specialized 3D printing applications grows, the development of new materials for SLA technology continues to evolve. Future trends in SLA 3D printing are driven by innovations in material properties and the introduction of emerging materials that will broaden the scope of what’s possible in manufacturing, healthcare, and beyond.
Emerging Materials
The future of SLA 3D printing is expected to see the rise of materials that cater to more specialized industrial needs. Key areas of development include:
- High-Performance Resins: These emerging resins are being designed for specific industries that demand parts with higher strength, heat resistance, or chemical resistance. For example, aerospace and automotive sectors will benefit from high-performance SLA resins that offer enhanced mechanical properties and durability under extreme conditions.
- Biocompatible and Bioresorbable Materials: As the healthcare sector increasingly adopts 3D printing, the development of new biocompatible resins is accelerating. In the future, we can expect more advanced materials for surgical guides, dental appliances, and even implants that degrade naturally in the body. This will allow for more personalized medical treatments and sustainable solutions.
- Sustainable and Eco-Friendly Resins: With a growing focus on environmental sustainability, research into eco-friendly resins is gaining momentum. These materials could be derived from renewable resources or designed to be biodegradable, reducing the environmental impact of 3D printing waste.
Innovations in Material Properties
In addition to the development of new materials, advancements in the properties of existing SLA materials are expected to push the technology forward. Innovations in material properties are focused on enhancing the performance and usability of SLA printing in various applications.
- Improved Toughness and Flexibility: While SLA materials are known for their precision, many traditional resins tend to be brittle. Future innovations will likely focus on improving the toughness and flexibility of SLA resins without sacrificing accuracy or surface quality. This will open up more applications where mechanical stress and impact resistance are essential.
- Multi-Material Printing: A key area of research is the development of SLA materials that can be printed simultaneously in a single print job. Multi-material printing would allow the combination of properties like rigidity and flexibility in a single part, enabling the creation of more complex, functional components without assembly.
- Smart Materials: Smart materials that can respond to environmental factors like heat, light, or pressure are on the horizon for SLA 3D printing. These materials could be used to create parts that adapt or change their properties in response to external stimuli, adding a new level of functionality and innovation to the technology.
As these emerging materials and innovations in material properties develop, the future of SLA 3D printing will continue to expand, offering even greater possibilities for industries ranging from manufacturing to medicine.
Why choose the SLA 3D printing method?
SLA printing has become the most widely used method of 3D printing because of the smooth surface and fine details the technology provides. Its high production quality and increased productivity has made the technology a staple in the UV additive manufacturing industry. SLA 3D printing is always a smart option.
Contact RAHN to get high-quality raw materials for 3D printing resins, customised to your industry needs.
Selecting the Right SLA 3D Printing Material for Your Needs
Choosing the right SLA 3D printing material ultimately comes down to understanding the specific requirements of your project. Whether you’re aiming for high detail, durability, flexibility, or biocompatibility, there’s an SLA resin tailored to your needs.
For prototypes and aesthetic models, standard resins provide a cost-effective solution with excellent detail and smooth surfaces. Engineering resins and tough resins are better suited for functional parts that require strength and resilience, while flexible resins offer versatility for parts that need elasticity. In the medical and dental fields, biocompatible resins ensure safety and regulatory compliance for patient-specific devices.
Don’t forget to factor in the post-processing requirements and cost considerations when making your choice. By carefully evaluating the demands of your project - whether it's mechanical performance, aesthetic quality, or specific regulatory needs - you can select the ideal SLA material to achieve the best results. This decision is key to maximizing both the efficiency and success of your 3D printing process.
Your personal contact
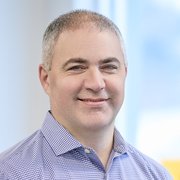
Christopher Cocklan
3D Printing Business Development Manager EnergyCuring
RAHN USA Corp.