A Guide to
DLP 3D Printing
A Guide to
DLP 3D Printing
A Guide to DLP 3D Printing
DLP 3D printing (digital light processing 3D printing) is a UV additive manufacturing technique that cures entire layers of photopolymer resins and is used where speed of production is critical. DLP 3D printing offers detailed, intricate models that are used for a wide variety of applications, including prototypes, 3D printed jewellery, dentistry or medical devices.
The following article gives you a thorough overview of the innovative printing technique, its possibilities and what kind of photopolymer resins are needed to create the desired results.
How does DLP 3D printing work?
DLP 3D printing (digital light processing 3D printing), along with others like material jetting, SLA printing, etc. is an additive manufacturing technique that uses light and photopolymers to create three-dimensional objects layer by layer.
The printing process uses a liquid photopolymer resin that hardens when exposed to light. A build platform is submerged or positioned just above a vat of the liquid photopolymer resin. The digital light projector shines UV light onto the resin, and the projected image corresponds to the first layer of the 3D object.
The areas of the photopolymer resin that are exposed to the UV light start to solidify or cure, while the uncured resin remains liquid.
The build platform is then incrementally lowered, allowing a new layer of liquid resin to flow over the cured layer. UV light is projected again to cure the new layer onto the previous one. This process of layer-by-layer curing and platform movement is repeated until the entire object is built.
Once the printing is complete, the object is typically still surrounded by uncured resin. It needs to be carefully removed from the build platform and to undergo post-processing steps, which may include rinsing, further curing under UV light as well as sanding, polishing or painting, depending on the desired finish.
Core Components of a DLP 3D Printer
- Build Platform: Supports the object during printing.
- Resin Vat: Contains the photopolymer resin.
- Light Source: Determines curing speed and print quality.
- DLP Projector: Controls the projection of UV light.
- Slicing Software: Converts 3D models into printable layers.
Advantages of DLP 3D printing
Compared to some other resin-based processes, DLP 3D printing offers advantages like faster print times, thanks to the simultaneous curing of each layer. At the same time, the level of detail and surface finish is still very high, making it suitable for applications that demand intricate and detailed objects.
DLP printers often come with user-friendly software interfaces, making them relatively easy to set up and operate.
The slicing software used for DLP printing allows for quick adjustment of parameters like layer height and exposure time. Some DLP printers offer relatively large build volumes, which enables the creation of larger objects in a single print. This can be advantageous for prototyping or producing larger parts.
DLP 3D printing enables the creation of highly customised objects, which is suitable for the production of highly-customizable one-off or low-volume production items.
DLP 3D printing applications
DLP 3D printing is commonly used in industries such as jewellery, dentistry and medical devices, where precise and detailed prototypes are crucial for testing and validation. Similarly, digital light processing 3D printing plays a crucial role in the healthcare industry. While DLP excels in high-precision applications, other 3D printing technologies, like 3D printing in construction, enable large-scale manufacturing for architectural and infrastructure projects.
Healthcare and Dental Applications of Digital Light Processing 3D printing
DLP 3D printing in healthcare is used, for instance, where precise dental models of patients' teeth and gums for treatment planning, orthodontic appliances, crowns, bridges and other dental applications are needed. On top of that, hearing aids and even anatomical models for medical education and surgical planning can be created with DLP 3D printing due to its high accuracy and resolution.
Applications in Dentistry
- Custom Dental Models: Used for treatment planning, orthodontic aligners, crowns, and bridges.
- Surgical Guides: DLP allows for precise, patient-specific templates to assist in complex dental procedures.
- Temporary and Permanent Restorations: Biocompatible resins enable functional, aesthetic dental prosthetics.
Applications in Medical Devices
- Hearing Aids: Digital light processing 3D printing is widely used for custom-fit, ergonomic hearing aids, reducing production time.
- Anatomical Models: Highly detailed organ and tissue models aid in medical training and surgical simulations.
- Medical Implants and Prosthetics: DLP printing supports customized prosthetics with biocompatible materials.
Digital Light Processing 3D Printing in Jewelry and Fashion
DLP 3D printing is revolutionizing jewelry design by allowing high-resolution, intricate detailing that was previously impossible with traditional handcrafting techniques. Designers can create complex patterns, filigree work, and organic shapes with unparalleled precision, significantly reducing the time and cost associated with mold-making.
Key Advantages for Jewelry Designers:
- Ultra-Fine Details: Enables micro-level precision for delicate designs.
- Castable Resins: Allows for direct investment casting, eliminating the need for traditional wax modeling.
- Custom and One-Off Pieces: Perfect for bespoke jewelry and rapid iterations before finalizing a design.
- Time Efficiency: Shortens prototyping cycles, allowing for quick market testing.
Applications in Engineering and Manufacturing
Digital light processing 3D printing has become a cornerstone technology in engineering and manufacturing, offering a rapid, cost-effective alternative to traditional prototyping methods. Its ability to quickly iterate designs and produce functional prototypes with high accuracy makes it an essential tool for automotive, aerospace, and industrial production.
Common applications are:
- Automotive Industry: Prototyping engine components, interior parts, and aerodynamics testing models.
- Aerospace and Defense: Manufacturing lightweight, high-strength parts for aircraft and drones.
- Consumer Electronics: Developing ergonomic and functional prototypes before mass production.
- Tooling and Molds: Creating high-precision molds for injection molding and small-batch production.
Advancing Bioprinting and Medical Research with Digital Light Processing 3D Printing
DLP 3D printing is paving the way for major advancements in medical research, tissue engineering, and bioprinting. Its ability to reproduce highly detailed anatomical structures makes it an invaluable tool for surgical planning, medical training, and the development of biocompatible implants.
Innovations in Bioprinting and Medical Research:
- Surgical Models: Doctors and medical students use 3D-printed organ models for pre-surgical planning.
- Bone and Cartilage Printing: DLP technology aids in custom prosthetics and regenerative medicine research.
- Drug Testing and Personalized Medicine: Researchers create miniaturized tissue structures to study disease behavior and test new drugs.
- Dental and Orthodontic Applications: DLP printing enables the production of clear aligners, crowns, and prosthetic components with biocompatible resins.
Requirements for DLP 3D printing materials
DLP printers can work with a wide range of photopolymer resins, each tailored to specific applications. This includes resins with various mechanical properties, colours as well as transparency levels.
The resin requirements for digital light processing 3D printing can be summarised as follows:
- Lower viscosity allows for fast and uniform recoating/refilling.
- Low shrinkage allows for little to no warping, which is especially important when it comes to fine details and larger structures.
- Avoid materials that will swell, cloud, or otherwise attack the window material.
DLP 3D printing vs. SLA 3D printing
Even though DLP 3D printing has a lot of similarities with SLA (Stereolithography) 3D printing, there are still major differences between the processes, which result in different applications that serve different requirements.
DLP 3D printing uses a digital light projector to project an entire layer of the object onto the surface of a vat, solidifying the liquid photopolymer resin according to the shape of the object. As each layer is cured, the build platform gradually moves upward, distancing the solidified layers from the resin vat.
On the other hand, SLA 3D printing employs a laser beam that moves across the surface of a vat filled with liquid photopolymer resin. For even finer precision and detailed microstructures, microstereolithography (MSL) offers enhanced capabilities.
The laser selectively cures specific points in the liquid resin, causing it to solidify at those points. As each layer is scanned and cured, the build platform also gradually moves upward to create the object layer by layer.
As a result of these processes, DLP printing is usually faster due to its ability to cure entire layers at once, whereas SLA cures point by point with a laser, making it generally slower. SLA prints often have a smoother surface finish, while DLP prints can be slightly more textured.
Some 3D printing resins formulated for SLA might not work optimally in DLP printers and vice versa, so it's important to choose the appropriate resin for your printer.
Comparison Table: Digital light processing 3D printing vs SLA
Feature | DLP 3D Printing |
SLA 3D Printing |
Speed |
Faster (cures layers at once) |
Slower (cures point-by-point) |
Resolution |
High, but slight pixelation |
Ultra-smooth detail |
Material Cost |
Depends on the resin used |
Depends on the resin used |
Ideal Applications |
Prototyping, dental, jewelry, engineering-grade prototypes |
Prototyping, dental, jewelry, engineering-grade prototypes |
DLP vs. Other 3D Printing Technologies (FDM, Material Jetting)
DLP 3D printing provides higher precision than FDM, making it ideal for intricate designs but at a higher material cost due to resin usage. Compared to Material Jetting, DLP is more affordable but lacks full-color and multi-material capabilities, making it best for functional, high-detail parts rather than aesthetic models.
- DLP vs. FDM (Better precision but higher cost).
- DLP vs. Material Jetting (More affordable, but jetting has higher color flexibility).
FAQ
1. How durable are digital light processing 3D printing parts?
Digital light processing 3D printing parts can be highly durable depending on the resin formulation. Engineering-grade resins provide high-impact resistance and mechanical strength, making them suitable for functional prototypes and industrial applications. However, all photopolymer resin 3D prints will require post-curing.
2. What are the limitations of digital light processing 3D printing?
While digital light processing 3D printing offers high precision and speed, it has some limitations:
- Limited build volume – Most DLP printers have smaller print areas compared to FDM, restricting large-scale production.
- Resin material constraints – DLP primarily relies on photopolymer resins, which may not have the same durability as metals or advanced thermoplastics.
- Post-processing requirements – Prints require washing, UV curing, and sometimes sanding or polishing for optimal strength and finish.
- Light exposure sensitivity – Some resins can degrade over time if not stored properly or exposed to prolonged UV light.
3. What are the requirements for materials used in DLP 3D printing?
DLP 3D printing materials must meet the following requirements:
- Low Viscosity – Ensures smooth flow and uniform layer recoating.
- Fast Curing Time – Allows for quicker print speeds and efficient layer bonding.
- Low Shrinkage – Reduces warping and ensures dimensional accuracy.
- High Resolution and Detail Retention – Supports fine features and smooth surfaces.
- UV Sensitivity – Must react efficiently to the projected UV light for proper curing.
- Mechanical Properties – Tailored to application needs (flexible, rigid, heat-resistant, or biocompatible).
Why choose the DLP 3D printing method?
DLP 3D printing is one of the fastest and at the same time a highly precise printing method to achieve great results and fast turnaround times.
We are experts in the field of photopolymers and our labs are equipped with industry-level SLA, DLP and LCD 3D printers, which enables us to develop custom solutions of raw materials for 3D printing that perfectly fit your needs.
Get in touch and book a call with our experts to find the best solution for your project.
Your personal contact
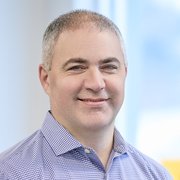
Christopher Cocklan
3D Printing Business Development Manager EnergyCuring
RAHN USA Corp.