3D Printing
for Wearable Technology
3D Printing
for Wearable Technology
3D Printing for Wearable Technology:
How Photopolymers Change the Manufacturing Landscape
Photopolymers have revolutionised the manufacturing landscape for wearable technology. Their unique properties, including high precision and diverse material capabilities, enable the creation of intricate and custom components for 3D printed wearables.
What Are Wearable Technologies?
Wearable technologies, often referred to simply as wearables, are electronic devices or accessories that can be worn on the body.
In most cases, these technologies establish connections between specific smart products, like smartwatches and smartphone applications. This allows users to access the intelligent features of these products from anywhere, as long as they have an active internet connection.
3D-printed wearable devices are designed to perform various functions, ranging from tracking health and fitness metrics to providing convenient access to information or communication. They have gained popularity in recent years due to advancements in technology and their potential to enhance daily life in a variety of ways.
Additionally, users have the ability to manage different functions of these wearable devices through their corresponding mobile applications.
What Are Examples Of 3D-Printed Wearable Technology
3D printing is revolutionizing the world of wearable technology, allowing for highly customized, lightweight, and functional designs. From fashion and accessories to medical applications, this technology is shaping the future of wearables in exciting ways. Here are some key examples of how 3D printing is being used in wearable technology today.
3D-Printed Smart Glasses and Eyewear
Additive manufacturing enables the production of custom-fit eyewear, designed for both style and functionality. 3D printing allows for complex frame designs, lightweight materials, and improved durability, making glasses more comfortable and personalized for users.
Customized Footwear and Insoles
manufacturers are leveraging 3D printing to create custom shoes and orthopedic insoles. These products are tailored to an individual’s foot structure, providing better support, improved comfort, and enhanced performance for athletes and individuals with medical conditions.
Wearable Medical Devices
Medical wearables, such as prosthetics, orthotic supports, and exoskeletons, are being 3D printed to ensure a precise fit for each user. This technology is making medical devices more accessible, reducing costs, and improving patient outcomes. Additionally, advancements in 3D printing in healthcare are expanding possibilities for wearable medical technology.
3D-Printed Fashion and Accessories
Designers are pushing the boundaries of fashion with 3D-printed jewelry, garments and accessories. This method allows for intricate patterns and sustainable production, as it minimizes material waste compared to traditional manufacturing techniques.
3D Printing for Wearable Technology: Applications and Usage
3D-printed wearables possess unique characteristics. The usage of custom-made photopolymers is ideal to fulfil the corresponding requirements, such as the demand for tensile and tear strength, a high degree of flexibility, low density and resistance to moisture and chemical. These properties are also critical in 3D printing in healthcare, where photopolymers are leveraged to create patient-specific devices and intricate medical tools.
Additive Manufacturing (AM) is a great choice for 3D-printed wearables. For instance, personalised running shoes have been successfully developed using AM and a marathon world record was achieved by an athlete wearing ultra lightweight footwear.
Common AM processes include Material Jetting (MJ), specifically Photopolymer Jetting (PJ) as well as Vat photopolymerization processes such as Stereolithography (SLA). SLA 3D printing materials have the ability to create highly detailed and intricate designs with exceptional precision. Photopolymers have the ability to create highly detailed and intricate designs with exceptional precision. This is especially important for 3D-printed wearables and devices, as they often involve small, precise components that need to fit together seamlessly.
Examples of 3D-Printed Wearable Devices and Products Manufactured With Photopolymers
Additive Manufacturing and custom photopolymers are mainly used to produce enclosures and housings, buttons and controls, straps and bands as well as optical components.
Enclosures and Housings
Photopolymers create finely detailed and precise structures, ensuring that the enclosures fit perfectly around the internal components of the wearable device. The smooth finish achieved with photopolymers contributes to the comfort and aesthetics of the products, as rough edges or surfaces can be prevented.
Buttons and Controls
Photopolymer-based 3D printers can work with multiple materials simultaneously. This allows for the creation of buttons with different properties, such as varying levels of tactility or feedback. Certain photopolymers can be transparent, making them suitable for creating clear or translucent buttons. This can be useful for wearables with displays or backlit controls.
Straps and Bands
Photopolymers can be engineered to possess a high degree of flexibility while maintaining durability, ensuring that straps and bands remain comfortable even during movement. Many photopolymers are biocompatible, meaning they are safe for direct skin contact. This is crucial for 3D-printed wearable devices, as users wear them for extended periods.
Optical Components
Optical components are used for display screens, lenses, and sensors, which require precision and clarity. Besides transparency, photopolymers can be engineered to incorporate anti-reflective coatings into these 3D-printed wearable devices, improving optical performance by reducing glare and reflections.
Advantages of Photopolymers for Wearable Technology
Photopolymers offer a lot of benefits in terms of material properties, production costs and process optimisation, which makes them an ideal choice for wearable technologies.
High Resolution and Detail
One of the standout advantages of using photopolymers in wearable technology is their capability to deliver high resolution and intricate detailing. This means that when crafting components such as enclosures, buttons, controls, straps, bands and optical elements, photopolymers excel in creating finely detailed and precisely engineered structures. This high level of precision ensures that 3D-printed wearables fit accurately, function seamlessly and offer an overall superior user experience
Diverse Material Properties
Photopolymers can be engineered to possess a wide range of characteristics, such as flexibility, durability, transparency and more. This versatility is invaluable in the production of wearables, as different components may require specific properties to function optimally. For instance, straps may need flexibility for comfort, while optical components may require transparency for clear display. This adaptability makes photopolymers a versatile choice for creating 3D-printed wearables with varying material needs.
Smooth Surface Finish
This characteristic is one of the benefits of 3D printing wearable technology, as it ensures a comfortable and polished feel when in contact with the user's skin. Additionally, the smooth finish enhances comfort and aesthetics, making it an ideal choice for wearables that require a sophisticated and user-friendly design.
Quick Curing Times
When exposed to the appropriate light source, photopolymers solidify swiftly, allowing for efficient and fast production processes. This speed is particularly advantageous in wearable technology development, as it enables manufacturers to create components and prototypes efficiently. Quick curing times with photopolymers contribute to streamlined production cycles and accelerated innovation.
Biocompatibility
Biocompatibility means that photopolymers can be engineered to be safe for direct contact with the skin after photopolymerisation. In wearable devices, where prolonged contact with the body is common, biocompatible photopolymers ensure that users can wear these technologies comfortably without the risk of skin irritation or adverse reactions. This property is crucial for creating wearables that are not only functional but also user-friendly and safe for extended use.
Reduced Tooling Costs
Using photopolymers offers a distinct advantage in terms of cost-effectiveness. Traditional manufacturing methods often require expensive moulds or tooling for production, which can be a significant upfront investment. In contrast, photopolymer-based 3D printing bypasses much of this tooling requirement, resulting in lower initial costs. This advantage is particularly beneficial for smaller-scale or customised production runs, where minimising expenses is essential for competitiveness and profitability.
Requirements of Photopolymers for 3D Printing Wearable Technology
3D-printed wearable devices have very specific material requirements, which need to be fulfilled to make the final product feasible. Depending on the composition, photopolymers are able to fulfil many of these requirements simultaneously.
Skin-Friendly Properties
Photopolymers used in wearables must be biocompatible, which means they should not cause irritation, allergies or any adverse reactions when worn for extended periods. This requirement is essential in creating wearables that prioritise user comfort and safety, making them suitable for long-term use without compromising skin health or well-being.
Chemical Resistance
Photopolymers must exhibit chemical resistance, which means that they should be able to withstand exposure to various substances, such as lotions, detergents and other chemicals commonly encountered in daily life. This property ensures that the material remains stable and does not degrade or react negatively when in contact with different compounds. By possessing good chemical resistance, photopolymers contribute to the overall durability and reliability of 3D-printed wearables.
Flexibility and Durability
Photopolymers must possess both flexibility and durability. These properties are crucial for creating components like straps, bands and enclosures that need to withstand movement and wear without becoming brittle or deformed. Flexibility ensures that wearables can conform comfortably to the contours of the body, providing a snug fit for the user. At the same time, durability ensures that these components remain intact and functional even under regular use and potential stress. Striking the right balance between flexibility and durability is essential in crafting 3D-printed wearables that are both comfortable and long-lasting.
Water and Moisture Resistance
3D-printed wearable devices should be capable of withstanding exposure to water, sweat and other forms of moisture without degrading or experiencing structural damage. This property is crucial for wearables, as they are often worn in various environments and may come into contact with liquids. Also, consumers are used to employing wearable technology during sports, so that water and moisture resistance is imperative for a wide range of wearables.
Compatibility with Electronics
Photopolymers must be compatible with electronic components to allow the devices to function effectively. This means that the material should not interfere with the functionality of sensors, circuits or other electronic elements integrated into the wearable device. Additionally, it should not cause electromagnetic interference or hinder signal transmission.
Photopolymers Enhance Wearable Technologies
The integration of photopolymers in wearable technology manufacturing marks a significant advancement. Their ability to provide high resolution, biocompatibility and diverse material properties has opened new frontiers in designing comfortable, precise and long-lasting wearables. This innovation paves the way for even more sophisticated and user-centric wearable devices in the future.
Contact us to find out more about our 3D printing solutions and how photopolymers can enhance your products.
Your personal contact
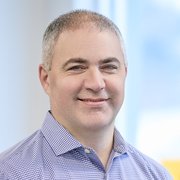
Christopher Cocklan
3D Printing Business Development Manager EnergyCuring
RAHN USA Corp.