3D Printing
in the Automotive Industry
3D Printing
in the Automotive Industry
Revolutionising Auto Manufacturing: 3D Printing in Automotive Industry
Faster prototyping, reduced costs, increased precision and customization – the automotive industry is evolving at an unprecedented pace. The latest trends revolve around 3D printing for automotive parts and its game-changing impact, which has the potential to shorten global supply chains while significantly reducing production time and resources.
The possible application scenarios are numerous and range from printing manufacturing aids to lightweight car parts.
In this article we are going to offer our readers a thorough bird’s-eye perspective about 3D printing in the automotive industry, its latest trends, common applications as well as potential obstacles to fully unleash the potential of Industry 4.0.
The Benefits of 3D Printing in Automotive Manufacturing
3D printing is revolutionising the prototyping and manufacturing processes of multiple industries, such as 3D printing in automotive industry, healthcare, mechanical engineering or the aerospace industry. We are currently witnessing the same trend in 3D printing for automotive parts.
While photopolymers were initially used for prototyping, we are already witnessing a change towards simple interior parts, such as clips or vent covers.
Industry experts predict that the photopolymer market will be able to produce functional mechanical parts, whose performance and durability will exceed required levels in the near future. At the current stage, photopolymers already contribute to faster prototyping, reduced costs, increased precision, sustainable processes as well as customization.
Faster prototyping
Prototyping is especially important in the automotive industry, as it entails lengthy stages, including design validation, pre-manufacturing and the actual prototyping stage. While most common manufacturing methods include vacuum casting or CNC manufacturing, 3D printing automotive industry is a method, which is primarily used at the beginning stages of the development process.
3D printing in the automotive industry uses various 3D resins to create complex and precise working models. This gives car manufacturers the benefit to quickly produce small prototypes, without the costs of expensive moulds and tooling. Further, the fast manufacturing process allows for iterations of the original design, without spending too many resources or waste materials.
Reduced costs
The investment of 3D printers usually recoups within a couple of months, as the length of the traditional prototyping process combined with tooling, material costs and numerous iterations requires a lot of time and resources. 3D printing for automotive parts allows for complex shapes and geometries. Expensive tooling or moulds can cost between thousands and even hundreds of thousands of dollars.
Next to the cost factor, an accelerated time to market means that producers can react to market changes and introduce new prototypes in hours instead of days and weeks. Overall, 3D printing in automotive industry offers greater design flexibility, faster turnaround times as well as huge cost savings that were previously impossible to achieve.
Increased precision
Precision in 3D manufacturing refers to the ability of the 3D printer to produce fine details. Nowadays, automobile manufacturers use 3D printing for automotive parts to produce complicated designs even in the initial production stages. For instance, Ford uses 3D printers to prototype the lettering of certain car models. Even though software is also able to produce digital prototypes, the printed sample still provides a clearer picture.
Increased precision requires advanced raw materials for 3D printing that feature, among others, heat resistance and durability. The reason is that even prototype parts need to endure the stress of the final products, which includes weather conditions, strong impacts as well as the internal heat emitting from the engine.
Sustainable processes
With the help of photopolymers, car manufacturers are able to innovate costly processes while reducing their costs by 3D printing automotive parts. Photopolymers made for the automotive industry already fulfil crucial material standards, such as FST (fire, smoke, toxicity) as well as ESD (electrostatic dissipative) certifications and are able to withstand heat and impact.
Further, 3D printing in automotive industry produces less waste and is usually more energy-efficient compared to traditional production. On top of that, the final parts are lightweight and contribute to less energy consumption of every produced vehicle.
Customization
3D printing for automotive parts offers the potential for mass-customization. This can range from single components and can lead to entirely customised vehicle designs. This new approach offers more flexibility to implement individual customer requirements to create a personalised vehicle – an approach, which to date is only open to very affluent customers.
Luxury manufacturers are already leveraging 3D printing in automotive industry to deliver bespoke solutions. Bugatti uses 3D printing to create highly customized brake calipers and interior elements, showcasing how the technology enables precision and creativity. Similarly, Audi has employed 3D printing for automotive parts, offering personalized dashboard trims and design accents tailored to customer preferences
Nowadays, it is already possible to create critical test components, such as gauges. Another advantage that boosts customization are the increased in-house capabilities, which go hand-in-hand with streamlined supply chains. More customization unleashes creativity among engineers and produces better results in shorter time frames. As we will see, the application possibilities are endless.
Applications of 3D Printing in Automotive Design
3D printing in the automotive industry offers a wide range of possibilities that concern virtually all components of the automobile. The following applications provide an insight about the huge potential offered by 3D printing for automotive parts.
3D printing of legacy parts
3D printing is invaluable when it comes to producing legacy parts, which are not readily available. Once the manufacturing cycle ends, authentic parts are usually available only on the secondary market, which increases the price and effort to find the right components. 3D printing of legacy parts is not only valuable for old-timers, but also outdated models.
Traditionally, manufacturers face challenges to provide customers with reasonably-priced one-off parts with no available tooling. 3D printing can change this dilemma, and even allow for customised modifications and improvements without the necessary tools. The digital model can easily be created with CAD software and immediately be produced without supply chain delays.
3D printing for digital inventory
3D printing in the automotive industry allows manufacturers to create a digital CAD library of critical spare parts that can be produced on demand. This digitalization of spare parts has numerous advantages for the automotive industry. First of all, warehouses can significantly reduce their sizes, stored spare parts and operating expenses across different locations.
A digital library further solves the problem of legacy parts, as all components are readily available in the library. Therefore, a digital library has the potential to reduce the amount and size of warehouses all over the world, as spare parts and components can easily be printed on demand.
3D printing for custom tooling
While a digital library solves the problem of storing, producing and distributing regular components, 3D printing has the potential to create fully customised parts and to accelerate the entire production process.
3D printing can create custom tooling devices such as fixtures, jigs and moulds, which already belongs to today’s best practices. For instance, Toyota’s automotive factories in Europe produce positioning jigs, fixtures and 3D printed seals to protect their engine parts. Custom tooling enables manufacturers to speed up the iteration and testing process, so that multiple versions can be created in a short amount of time.
3D printing for lightweighting car parts
The term “lightweighting” refers to an own category in car manufacturing, which aims at producing lighter cars without sacrificing performance or safety. This comes with several advantages, such as reduced emissions and an improved fuel-efficiency. Developing high-performing as well as lighter parts is a complicated process, which needs to make use of modern manufacturing technologies.
3D printing for automotive parts is a promising manufacturing process, which enables designers to develop lightweight solutions with plastic components as well as composite materials. The results are complex geometries that are lighter than traditional parts without compromising performance and durability. Depending on the specific component, material costs can also be saved.
3D printed moulds
Moulds in traditional manufacturing require a lot of resources, which gives car manufacturers less flexibility when it comes to making changes once the moulds are designed. The costs are significant: Moulds can cost between thousands and hundreds of thousands of dollars. Further, a car may require dozens of moulds for various components.
Moulds made from 3D printing can be used for a wide range of materials, including plastics or metals. 3D printing has the potential to streamline this previously expensive and time-consuming process by only using a fraction of the resources. Designers are also able to make further iterations once the moulds are finished.
3D printed manufacturing aids
Manufacturing aids are tools, fixtures, moulds and a wide range of other devices that are used to improve the manufacturing process as well as related processes, such as quality control. While manufacturing aids serve a different purpose than regular car components, they still need to fulfil similar quality standards, such as reliability, effectiveness and safety.
Process engineers have more flexibility to design, create, and iterate individual components to optimise all stages of the manufacturing process. These aids enhance production efficiency by reducing setup times, ensuring precise assembly, and minimizing errors, which ultimately speeds up the overall manufacturing cycle. This improves efficiency as well as accuracy and reduces time and costs of the overall process.
Challenges: The potential hurdles and limitations of 3D printing in the automotive industry
Even though 3D printing in automotive industry has a promising future and will further streamline manufacturing processes around the world, there are still hurdles and limitations to overcome, as 3D printing is only a few decades old, while traditional manufacturing has gone through centuries of optimization.
As a result, there are still limitations when it comes to materials used in 3D printing, which probably is one of the biggest obstacles. 3D printing doesn’t have the capability of processing some of the materials used in traditional processes, which in turn limits its applications. Further, many printers still have size limitations, so that not all components can be produced in smaller-sized models.
Material Limitations
The 3D printing in automotive industry faces significant challenges when it comes to materials. While the technology is innovative, it still cannot process many high-performance materials used in traditional manufacturing. For instance, advanced metals and composites necessary for durable automotive parts are limited in availability for 3D printers. This restricts the full potential of 3D printing for automotive parts in high-stress applications like engine components and structural parts.
High Costs for Advanced Materials
Despite its efficiency, 3D printing in the automotive industry struggles with the high cost of advanced materials. Specialized materials such as carbon fiber composites and high-temperature-resistant polymers offer great benefits but come at a premium price. This makes 3D printing for automotive parts less viable for large-scale manufacturing, limiting its use to prototyping and custom projects.
Scalability Challenges in 3D Printing in the Automotive Industry
A major challenge for 3D printing in automotive industry is scalability. While ideal for prototypes and low-volume production, the technology lacks the speed and cost-efficiency needed for mass production. Traditional manufacturing methods like injection molding are still more effective for producing thousands of identical parts. To scale effectively, combining 3D printing for automotive parts with traditional methods is being explored as a hybrid solution.
Quality Consistency in Large Volumes
Maintaining consistent quality is crucial for the 3D printing in automotive industry, especially for large-scale production. Variations in printer calibration, material properties, and environmental conditions can impact the uniformity of parts. For automotive parts, where precision and reliability are essential, this inconsistency poses a significant challenge. Advanced quality control systems are being developed to ensure that 3D-printed parts meet the stringent standards of the automotive sector.
Conclusion: The future of 3D printing in the automotive industry
3D printing in the automotive industry offers the potential to rethink a decades’ old industry. Warehouses and spare parts can be replaced all over the world with a centralised digital inventory as well as local 3D printers. Global supply chains can be reduced to a fraction of the current status, while resources and time to market will drastically decrease.
Customers will be able to order customised vehicles instead of one-size-fits-all solutions, taking into account each individual preferences and budgets. 3D printing for automotive parts therefore opens a new chapter of customization and accelerates industry 4.0, for faster times to market, new creative inputs and custom-made solutions.
Your personal contact
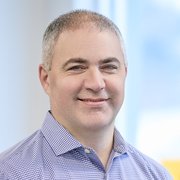
Christopher Cocklan
3D Printing Business Development Manager EnergyCuring
RAHN USA Corp.