Ceramic Resin
3D Printing
Ceramic Resin
3D Printing
Features and Ways of Using Ceramic Resins
The photopolymerization of ceramic resins offers a new approach to a traditional craft.
- Intricate, high-quality products
- A distinct look and feel
- A fraction of the costs and production times compared to traditional ceramic processing
- Valuable properties (stiffness, thermal resistance, electrical insulation and more) for a wide range of applications
Find out more about ceramic resins, their main properties and applications, and how your business can profit from ceramic resin 3D printing.
What Are Ceramic Resins?
UV-curable ceramic resins are a type of UV curable resin for 3D printing that cures (hardens) when exposed to ultraviolet (UV) light. These resins are considered a composite material, which usually entails monomers, oligomers, photoinitiators as well as additives. When exposed to UV light, the photoinitiators undergo a process called photopolymerization, which causes the monomers and oligomers to cross-link and form a solid, ceramic-like material.
The outcome presents a unique, uniform matt finish that offers a ceramic look and feel. This adds a refined touch to any 3D printed piece, distinguishing it from those made from other materials.
UV-curable ceramic resins offer several advantages over traditional ceramic materials and other types of resins. They cure rapidly when exposed to UV light, allowing for faster production processes. UV curing enables precise control over the entire process, resulting in high-resolution prints with intricate details.
Ceramic resins can be customised to achieve specific material properties such as strength, hardness, and thermal stability. Applications of UV-curable ceramic resins include heat-resistant applications, decorative items, prototypes, dental industry, automotive, aerospace and medical applications.
The Difference between Oxides and Non-Oxides Ceramic Resins
When it comes to ceramic resins, there are two main distinguishable groups: oxides and non-oxides.
Oxide ceramic resins contain ceramic particles composed primarily of metal oxides, such as alumina (Al2O3), zirconia (ZrO2), or silica (SiO2). Oxide ceramic resins are known for their excellent mechanical properties, including high strength, hardness, thermal stability and the ability to withstand oxidation. They are commonly used in applications requiring robust and durable ceramic materials, such as aerospace components, automotive parts, and cutting tools.
Non-oxide ceramic resins, on the other hand, contain ceramic particles composed of non-metallic elements, such as carbides, nitrides, and borides. Examples of non-oxide ceramic materials include silicon carbide (SiC), silicon nitride (Si3N4), and boron carbide (B4C). Non-oxide ceramic resins offer advantages such as high hardness, wear resistance, and excellent chemical stability. They usually perform better in extreme environments and show a high level of corrosion resistance, hardness, and oxidation resistance.
The Main Properties of Ceramic Resins
Ceramic resin 3D printing is becoming more popular due to the valuable properties, ranging from high stiffness, thermal resistance as well as a distinct look and feel of the final product.
High Stiffness
Ceramic resins are characterised by their exceptional stiffness, offering superior resistance to deformation and bending. This high stiffness makes them highly desirable for various industrial applications, where stability and durability are critical requirements, including aerospace, automotive, electronics as well as medical devices.
Great Thermal Resistance
Depending on the specific formulation and application requirements, ceramics can withstand very high temperature. For instance, silicon carbide and silicon nitride are commonly used ceramics that can withstand temperatures of up to 2400 degrees Celsius, making them the ideal choice in extreme thermal environments.
Electrical Insulation
Ceramic resins offer superior electrical insulation due to their non-conductive nature, effectively preventing the flow of electricity. This property makes them valuable in electrical and electronic components, such as circuit boards, insulators and encapsulation materials, where maintaining electrical integrity and safety is paramount for reliable operation.
Distinct Look and Feel
Ceramic resins have a distinct look and feel characterised by their smooth surface finish and tactile quality. Their appearance often mimics that of traditional ceramics, with the added benefit of being customizable in terms of colour, texture and surface details, offering unique aesthetic possibilities in various applications.
Applications of Ceramic Resin 3D Printing
Ceramic resin 3D printing has found diverse applications across several industries due to its ability to produce intricate parts with high precision and customization.
- 3D printing in the automotive industry as well as aerospace requires heat-resistant applications. Ceramic resin 3D printing is utilised to create components that can withstand extreme temperatures and harsh environmental conditions.
- In wind tunnel testing, ceramic resin 3D printing is employed to fabricate accurate and durable models for aerodynamic studies.
- In the decorative items industry, ceramic resin 3D printing enables the production of unique and customised ceramic art pieces, pottery, and home decor items with intricate designs and textures.
- Within the dental industry, ceramic 3D printing in dentistry is used to fabricate dental prosthetics, crowns and bridges with precise fit and aesthetic qualities.
- When it comes to 3D printing in healthcare, ceramic resins are utilised to manufacture lightweight yet durable components, such as implants and surgical guides, where high strength, biocompatibility and heat resistance are crucial requirements.
Methods of Ceramic Resin 3D Printing
Ceramic resin 3D printing encompasses several methods that enable the fabrication of ceramic parts. Each of the following ceramic resin 3D printing methods has its own advantages and limitations, offering different levels of resolution, speed, and material properties. The choice of method depends on the specific requirements of the application, such as desired part size, complexity, surface finish and material properties.
- Stereolithography (SLA): This technique involves curing liquid ceramic resin layer-by-layer using a UV laser. SLA offers high resolution and surface finish, making it suitable for creating intricate ceramic prototypes and small-scale components with fine details.
- Material Jetting: Material Jetting is another method where ceramic resins are jetted onto a build platform layer-by-layer using print heads similar to inkjet printers. This method enables the production of complex ceramic parts with varying material properties and colours, making it useful for creating decorative items and prototypes.
- Digital Light Processing (DLP): This method involves curing ceramic resin with UV light projected from a digital light projector onto a build platform. DLP offers fast printing speeds and high resolution, making it suitable for 3D printing for jewellery, producing dental prosthetics, and other small-scale ceramic parts.
Add Value to Your Products With RAHN’s Raw Materials for Custom Ceramic Resins
Unlock new possibilities for your products with RAHN’s custom ceramic parts. Our innovative 3D printing solutions empower you to enhance performance, durability and aesthetics of your products. Contact us today to discover how our ceramic resins can add value to your projects.
https://www.sciencedirect.com/topics/materials-science/silicon-nitride
Your personal contact
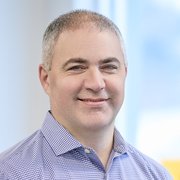
Christopher Cocklan
3D Printing Business Development Manager EnergyCuring
RAHN USA Corp.