Photopolymers in
UV Addititve Manufacturing
Photopolymers in
UV Addititve Manufacturing
UV Curable 3D Printing – The Significant Role of Photopolymers
UV 3D printing methods make use of liquid photopolymers to create physical objects. What are these methods and why are photopolymers a game changer in modern manufacturing, especially in the UV additive manufacturing? We are going to take a look at the most commonly used UV cure 3D printing methods and their most crucial components – photopolymers.
What is Photopolymer Resin?
Photopolymer resin is a liquid material that solidifies when exposed to ultraviolet (UV) light, making it essential for UV 3D printing. It is widely used in technologies like SLA (Stereolithography, Microstereolithography) and DLP printing, where the resin is cured layer by layer to create detailed, high-resolution objects. UV curable resin for 3D printing is known for its smooth surface finish and ability to produce intricate designs, making it popular in industries such as jewelry, dentistry, and prototyping.
The resin is composed of monomers, oligomers, and photoinitiators, which react to UV light through a process called photopolymerization.
This allows photocurable resins for 3D printing to be tailored for different properties like rigidity, flexibility, or impact resistance, providing versatility across multiple industries.
In 3D printing photopolymer resin, the result is an efficient production process that requires minimal post-processing and supports rapid prototyping as well as functional part creation.
Benefits of 3D Printing Photopolymer Resin
3D printing with photopolymer resin offers several advantages, particularly for applications that require high precision and smooth surface finishes. Some key benefits include:
- High Accuracy and Detail: Resin-based 3D printers are known for their exceptional accuracy, capable of producing intricate details that are difficult to achieve with other 3D printing methods. This makes photocurable resins for 3D printing ideal for applications like dental models, jewelry, intricate prototypes, and 3D-printed wearable devices, which require high precision and customizability.
- Smooth Surface Finish: One of the standout benefits of 3D printing photopolymer resin is the smoothness of the finished product. Due to the fine layer resolution and the curing process, parts printed with resin require minimal post-processing to achieve a polished appearance.
- Versatility in Material Properties: Photopolymer resins can be formulated to achieve a wide range of material properties, from rigid and tough to flexible and rubber-like. This versatility allows industries to select resins tailored to specific requirements such as flexibility, durability, or even biocompatibility for medical applications.
- Fast Printing Speeds: Resin 3D printers, especially those utilizing DLP or MSLA (Masked Stereolithography), can cure entire layers at once, resulting in faster print times compared to traditional filament-based printing methods. This efficiency is particularly useful in rapid prototyping or large-scale production.
Limitations of 3D Printing Photopolymer Resin
While 3D printing with photopolymer resin offers many advantages, there are several limitations to consider:
Certain Resins Might Be Fragile
One of the major drawbacks of standard photocurable resins for 3D printing is their tendency to be brittle once cured. This fragility can limit their use in applications requiring impact resistance or flexibility. For instance, if exposed to stress or dropped, resin parts may crack or shatter. While there are specialized resins available that provide improved durability or elasticity, they typically come at a higher cost and may not be suitable for all applications.
Post-Processing May Be Necessary
Photopolymer resin prints often require post-processing to achieve the final desired quality. After the initial printing, parts must typically be cleaned in isopropyl alcohol to remove excess uncured resin. Additionally, many parts require further curing under UV light to fully harden. This adds extra steps and time to the production process, which can be inconvenient for users seeking quick turnaround times. Moreover, careful handling is necessary during these stages to avoid damaging the prints.
What is UV 3D printing?
UV 3D printing relies on photopolymerization to build the desired objects layer by layer. Common printing methods include Stereolithography (SLA), Digital Light Processing (DLP) as well as Continuous Liquid Interface Production (CLIP) and MultiJet Modeling (MJM).
Even though the processes differ, a common feature of these types of UV additive manufacturing is the use of a liquid photopolymer resin, which is sensitive to ultraviolet (UV) light - such as UV curable resin for 3D printing.
When the printing process starts, the liquid resin is selectively exposed to UV light, which makes it solidify.
UV 3D printing with photopolymers is able to produce high-resolution and detailed objects, while speeding up production time and reducing material waste. Therefore, the technology finds applications in various industries, including 3D printing in healthcare, 3D printed jewellery, UV additive manufacturing in aerospace and 3D printing in the automotive industry.
Preparing 3D Prints for Curing
When working with UV 3D printing, preparing your 3D prints for curing is a crucial step to ensure the final product reaches its full potential in terms of durability and appearance. Here is a step-by-step guide to getting your prints ready for UV cure 3D printing:
1. Cleaning the 3D Print
After the printing process, the first step is to clean your 3D print to remove any excess resin. This typically involves using isopropyl alcohol (IPA) or another cleaning solvent. Gently submerge the print in a bath of IPA and use a soft brush to remove any uncured resin from the surface. Make sure to clean intricate areas or crevices where resin might collect, as this can affect the curing process and final quality.
Action Tip: Rotate the print in the solvent to ensure even coverage and thorough cleaning. Use multiple rinses if necessary for heavily detailed prints.
3. Setting Up for UV Exposure
Once your print is cleaned and checked for defects, it's time to set it up for the UV cure 3D printing process. Place your 3D print on a rotating platform or in a UV curing chamber to ensure even exposure to UV light. Depending on the size and thickness of the object, curing time may vary, so it’s essential to monitor the process closely.
Action Tip: Ensure the print is exposed evenly to UV light by either rotating it manually or using a curing station with built-in rotation. This will help achieve a consistent cure across the entire model.
2. Checking for Defects
Before moving on to curing, carefully inspect the 3D print for any defects such as cracks, warping, or imperfections that might have occurred during the printing process. Address these issues before curing, as defects can be harder to fix once the resin has been fully cured.
Action Tip: Minor defects or imperfections can be smoothed out with fine sandpaper or carefully removed with precision tools. Fixing these issues now will improve the final result post-curing.
4. Curing Time
The duration of the UV curing process will depend on the resin type, the intensity of the UV light source, and the thickness of the 3D print. Typically, curing can take anywhere from a few minutes to several hours. Overcuring can make the material brittle, while undercuring may result in a soft or tacky surface, so it's essential to find the optimal curing time for your specific resin.
By following these steps, you can ensure your 3D prints are clean, defect-free, and properly prepared for UV cure 3D printing, resulting in stronger, higher-quality parts.
Common methods of UV cure 3D printing
UV curable 3D printing uses different methods to create physical objects. The most common methods of UV additive manufacturing include SLA, DLP, CLIP and MJM.
Stereolithography (SLA)
Stereolithography (SLA) is one of the most widely used UV additive manufacturing methods for creating 3D objects using a layer-by-layer approach, which is particularly known for its ability to produce high-resolution and highly detailed 3D prints.
The SLA 3D printing process starts with a 3D digital model of the object to be printed. This digital model is created using computer-aided design (CAD) software or obtained through 3D scanning techniques. The printer consists of a vat or tank filled with liquid photopolymer resin.
Wherever the UV light strikes the resin, it causes the photopolymerization reaction to occur. During this process, the liquid UV curable resin for 3D printing solidifies and transforms into a hardened, solid material. The build platform is then incrementally raised, allowing the next layer of the object to be printed on top of the previous one. This layer-by-layer building process continues until the entire 3D object is complete.
Post-processing steps are typically required to clean and finalise the printed object. These steps often involve rinsing the object in a solvent or isopropyl alcohol to remove any remaining liquid resin. The object may also undergo additional UV light exposure to ensure complete curing and hardening of the material
Digital Light Processing (DLP)
Digital Light Processing (DLP) is similar to stereolithography (SLA) in the sense that it uses photopolymer resin layer by layer to create 3D objects. The key difference lies in the way the UV light is used to solidify the resin during the printing process.
In DLP 3D printing, the printing process starts with a 3D digital model of the object to be printed. While the digital model design is similar to SLA, the difference lies in the photopolymerization process. Instead of using a laser, DLP printers use a digital micromirror device (DMD) or an array of micromirrors.
These mirrors project UV light onto the entire layer of the object. By doing so, the process solidifies the entire layer in one exposure, unlike point-by-point scanning in SLA. This exposure of a complete layer allows DLP printers to achieve faster printing speeds. Digital Light Processing has become a popular UV additive manufacturing method due to its speed and efficiency in producing 3D prints with high resolution and fine details.
Continuous Liquid Interface Production (CLIP)
Continuous Liquid Interface Production (CLIP) is an innovative 3D printing technology developed by Carbon3D (also known as Carbon Inc.). CLIP represents a significant advancement in the speed and quality of 3D printing compared to traditional approaches like stereolithography (SLA) and digital light processing (DLP), as it utilises a combination of UV light and oxygen to create objects from a liquid photopolymer resin.
Unlike layer-by-layer approaches in most UV additive manufacturing technologies, CLIP works continuously, without the need for a build platform to move incrementally after each layer is cured. After the CAD model is finished, the CLIP 3D printer projects a sequence of UV images onto a transparent, oxygen permeable window. Between the window and the object being printed lies the "dead zone", a very thin layer of resin that never solidifies, as oxygen diffuses through the window.
Inside this dead zone, the polymer resin is exposed to UV light, causing it to photopolymerize and solidify at the interface between the liquid resin and the window.
At the same time, oxygen is selectively introduced into the dead zone, creating a thin, liquid interface between the solidified part and the rest of the resin.
The key innovation of CLIP lies in the continuous movement of the build platform, which lifts the object upward out of the liquid resin pool. As the build platform rises, the object is continuously pulled from the liquid resin bath while the liquid interface solidifies, forming the desired 3D shape. This continuous process allows for faster printing speeds compared to traditional layer-by-layer techniques.
MultiJet Modeling (MJM)
MultiJet Modeling (MJM) is a 3D printing technology developed by 3D Systems and known for its ability to produce highly detailed and accurate models with a smooth surface finish. The MJM process uses multiple printheads to precisely deposit droplets of liquid photopolymers layer by layer onto a build platform.
Once a layer of the model is printed, UV light is used to instantly solidify the material. Then, the next layer is deposited, and the process repeats until the entire model is completed.
The ability to use different materials and colours in a single printing process allows for the creation of realistic prototypes and models useful in various applications, such as design, product development or the medical field and dental industry.
More information about Additive Manufacturing: What is Material Jetting?
Photopolymers: The main ingredient of UV 3D printing
Photopolymers make UV additive manufacturing possible. Vat photopolymer UV curable resins for 3D printing are available in a wide range of formulations, each with unique material properties. The main ingredients are monomers/oligomers, photoinitiators as well as additives.
Monomers/Oligomers
Monomers can be compared to building blocks of photopolymer resins. They are small, molecular units capable of forming chemical bonds with other monomers. In their liquid state, photopolymer UV curable resins for 3D printing consist primarily of monomers. These monomers are designed to have specific chemical properties, such as low viscosity and high reactivity to light.
Oligomers, on the other hand, are larger molecules formed by the combination of several monomers through chemical bonding.
They contribute to the overall mechanical properties, strength, and durability of the UV additive manufacturing object.
By controlling the different types and ratios of various oligomers, manufacturers can fine-tune the characteristics of the final printed part. The selection of monomers and oligomers in photopolymers is therefore crucial in achieving specific material properties, such as flexibility, rigidity, toughness, or transparency
Photoinitiators
Photoinitiators are typically organic compounds that are sensitive to specific wavelengths of UV light, a critical aspect of UV additive manufacturing. When the photoinitiators absorb UV light of the appropriate wavelength, they undergo a photochemical reaction that generates highly reactive species, depending on the type of photoinitiator used.
These reactive species initiate the polymerization process by breaking the chemical bonds in the monomers and oligomers present in the UV-curable 3D printing resin. As a result, the monomers and oligomers start to link together, forming long chains called polymers.
This cross-linking of molecules leads to the solidification of the liquid resin, resulting in the desired 3D printed object.
Photoinitiators are chosen carefully to match the specific UV light source used in the 3D printer. Different photoinitiators have different absorption spectra, meaning they are sensitive to different ranges of UV light wavelengths. Therefore, the selection of an appropriate photoinitiator ensures efficient and controlled photopolymerization under specific UV light exposure conditions.
Additives
Additives are various substances that are incorporated into the polymer formulation to modify its properties. Each additive serves a specific purpose, and the overall formulation must be optimised to achieve the desired properties in the final product.
Stabilisers are additives that are used to prevent degradation of the polymer during storage or under prolonged exposure to light, while plasticizers are used to increase the flexibility and reduce the brittleness of photopolymers.
Other additives such as pigments and dyes are used to impart colour or opacity to photopolymers, making them more aesthetically appealing or functional for specific uses. In some applications of UV additive manufacturing where fire resistance is essential, it is even possible to add flame retardants to photopolymers in order to reduce their flammability and enhance safety.
The Importance of UV Curing in 3D Printing
UV 3D printing is a transformative process that enables precise and rapid production of high-quality 3D objects. One of the key elements in this process is UV curing, where ultraviolet light is used to harden the photopolymer resin layer by layer. This curing process is critical in determining the final quality, durability, and overall performance of the printed object. UV cure 3D printing allows for faster production cycles, improved material properties, and reduced post-processing, making it a vital aspect of resin-based 3D printing methods like SLA and DLP.
UV 3D Curing: Leveling Up Quality and Durability
The UV cure 3D printing process directly impacts the mechanical strength and durability of the finished product. UV curing allows for more consistent hardening of the material, resulting in uniform parts that are less likely to warp or deform over time. Additionally, the ability to control the exposure of UV light helps improve the precision and accuracy of fine details in the print, enhancing overall part quality. This process not only strengthens the final product but also enhances its surface finish, giving it a polished, professional look.
Material Versatility and Reduced Post-Processing:
One of the significant advantages of UV 3D printing is its compatibility with a wide range of materials. Photopolymer resins can be tailored for specific properties, such as flexibility, rigidity, or even biocompatibility, making UV 3D printing adaptable to various industries. Additionally, the precise curing provided by UV light often minimizes the need for extensive post-processing. The clean surface finishes and fine details achieved with UV curing reduce the time spent on sanding, polishing, or additional treatments.
Real-Time Adjustments and Automation:
Incorporating UV curing into the 3D printing process allows for real-time adjustments during production. Automated systems can modify UV exposure to optimize curing for specific layers, ensuring the material properties remain consistent throughout the print. This level of control improves the overall efficiency of the UV 3D printing process, allowing manufacturers to deliver higher-quality parts with fewer defects or inconsistencies.
Energy Savings and Sustainability:
UV cure 3D printing is also recognized for its energy efficiency. UV curing systems are designed to use less power while achieving faster curing times compared to traditional heat-based curing processes. This results in significant energy savings, making it a more sustainable option for large-scale production. Additionally, UV curing produces less heat, reducing the environmental impact and ensuring a safer working environment.
Precision and Efficiency:
The precision of UV 3D printing is unmatched when compared to other printing technologies. By curing entire layers at once, as seen in DLP printing, the process delivers faster build times without compromising accuracy. The precise application of UV light allows for the creation of intricate geometries and smooth surfaces, making it ideal for industries that require high levels of detail, such as dentistry, jewelry, and prototyping. The efficiency of UV curing also extends to shorter production cycles, enabling quicker time-to-market for businesses.
The final product of UV 3D printing depends on the right choice of photopolymers
Next to the right production process, the choice of photopolymers is crucial to create high-quality 3D prints that fulfill all requirements. RAHN is your provider of raw materials for 3D printing, including materials suitable for UV additive manufacturing, and develops custom photopolymers for every purpose.
We are experts in the field of photopolymers and our labs are equipped with industry-level SLA, DLP and LCD 3D printers, which enables us to develop custom solutions that perfectly fit your needs.
Get in touch and book a call with our experts to find the best solution for your project.
FAQ
How to tell if UV resin is cured?
To tell if UV resin is fully cured, there are several key indicators to check:
- Surface Hardness: A fully cured UV resin should feel hard and solid to the touch. Press your fingernail gently against the surface. Any sticky or soft areas indicate that the resin requires more UV exposure.
- Transparency: If your resin is transparent, check its clarity. A properly cured UV resin will be clear and free of cloudiness. Any haziness could mean that the resin is undercured or trapped air bubbles still need to be addressed.
- Color Consistency: Cured resin should maintain an even color throughout. Discoloration or uneven spots may suggest incomplete curing, particularly in thicker areas where UV light might not have penetrated evenly.
- Brittleness: While UV resin should be solid, it shouldn’t be overly brittle. If it cracks easily, it might be overcured, especially if it has been exposed to UV light for too long. These factors can help you determine whether your UV resin is fully cured or needs additional UV light exposure for optimal results.
Why is my UV resin sticky after curing?
Several factors can cause UV resin to remain sticky after curing, but the primary reason is inadequate UV light exposure, which prevents full curing of each layer. Another possible cause is "oxygen inhibition," where the resin's surface remains tacky due to contact with oxygen during the curing process.
Are UV curable resins for 3d printing environmentally friendly?
Photopolymer resins are indeed pollutants that can harm marine life and disrupt ecosystems if not handled properly. Liquid resin is particularly hazardous, as it can leach toxic chemicals into water sources. However, fully cured UV resin is less harmful to the environment, as the curing process solidifies the material, reducing its toxicity and making it safer for disposal. Still, proper disposal methods should be followed to minimize environmental impact.
Your personal contact
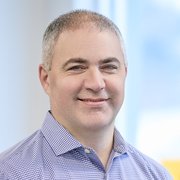
Christopher Cocklan
3D Printing Business Development Manager EnergyCuring
RAHN USA Corp.