What is
Vat Photopolymerization?
What is
Vat Photopolymerization?
What is Vat Photopolymerization?
A Guide to the process and its most common forms
Vat Photopolymerization is an advanced 3D printing technique that creates highly detailed objects by curing liquid resin with light, layer by layer.
In this article, we'll explore the Vat photopolymerization process and its most common forms, including SLA, DLP, and LCD.
What is Vat Photopolymerization?
Vat photopolymerization, often referred to as VPP, is a 30+ year old method of 3D printing that utilizes a light source to selectively harden photoreactive resin, also known as photopolymers.
The process involves a vat (a shallow container) filled with liquid 3D printing resin. A light source, such as a laser or a digital light projector (DLP), cures the resin layer by layer. The build platform moves incrementally after each layer is cured, allowing new resin to flow over the previously solidified layer.
The 3D printing resin is held in a vat either above or below the light source.
- In top down printing, the build plate remains submerged below in the resin tank and sequentially lowers when each successive layer is cured.
- In bottom up printing, the build plate is suspended above the vat, and the light is projected through a film, or window, on the bottom.
Vat photopolymerization is known for its extremely good resolution and accuracy.
The Vat Photopolymerization process
The following steps describe the entire photopolymerization process in Additive Manufacturing (AM):
1. Preparation of the Design: A digital 3D model is designed using CAD software, while slicing software guides the printer during the printing process.
2. 3D Printer Setup: A photopolymer is chosen according to the desired properties (e.g., flexibility, durability). The vat printer is calibrated, including proper levelling of the build platform and resin temperature adjustment if required.
3. Filling the Resin VAT: The vat is filled with liquid photopolymer resin. The resin must remain uncontaminated and free of bubbles.
4. Light Curing Layer by Layer: A light source selectively cures the resin layer by layer. The resin in the exposed areas solidifies.
5. Layer-by-Layer Repetition: After each layer is cured, the build platform moves slightly, allowing fresh resin to flow over the cured layer. This step is repeated until the entire object is formed, with each layer bonding seamlessly to the previous one.
6. Post-Printing & Post-Curing: The printed object is detached from the build platform and uncured resin is removed. The object is placed in a UV curing chamber to complete the polymerisation process.
7. Finishing: The surface can be further polished, painted and coated to improve aesthetics.
Advantages of Vat Photopolymerization
Vat photopolymerisation offers numerous advantages, which makes it a preferred choice for high-precision 3D printing and detailed prototyping.
- High Precision and Detail: Vat photopolymerisation delivers exceptional accuracy. This makes it ideal for creating intricate designs and detailed prototypes.
- Smooth Surface Finish: The process produces parts with superior surface quality, reducing the need for extensive sanding or polishing in post-processing.
- Material Versatility: A wide range of resins are available with different properties such as flexibility, durability, heat resistance, and biocompatibility, to suit various applications.
- Customisation: The technology allows for the creation of complex geometries and bespoke designs.
- Speed for Prototypes: Particularly in DLP systems, entire layers can be cured simultaneously, speeding up the process for smaller, detailed objects.
- Minimal Waste: Unused resin in the vat can be reused, which results in efficient material usage and less waste compared to subtractive methods.
- Wide Application Range: The method is commonly used in industries such as dentistry, orthopaedics, jewellery, and precision engineering due to its adaptability.
Most common types of Vat Photopolymerization
Vat photopolymerisation includes several methods, each suited to specific applications. The most common types SLA, DLP, and LCD differ in their curing technologies and offer unique advantages in precision, speed, and cost-effectiveness
LCD
For low to medium-volume production, Liquid Crystal Display (LCD) printing offers an excellent entry point into Vat photopolymerisation. It uses an LCD screen to selectively block or transmit UV light, curing the resin layer by layer. The screen works in tandem with a UV light source to create patterns that solidify the material.
LCD printing is often favoured for desktop 3D printers due to its affordability and accessibility. It provides good resolution, which makes it suitable for hobbyists and small businesses without the higher costs of SLA or DLP systems. While LCD printing is efficient and budget-friendly, it can have limitations in durability and print consistency.
DLP
Digital Light Processing (DLP) is a faster alternative to SLA, using a digital projector to cure entire layers of resin simultaneously. Instead of tracing each layer with a laser, the projector flashes a pattern of UV light onto the resin surface, curing it in one go.
DLP printers are well-suited for creating small to medium-sized objects with high resolution. The speed of the process makes it advantageous for time-sensitive projects, such as rapid prototyping. DLP also offers excellent detail quality, comparable to SLA.
One limitation of DLP is that the resolution depends on the size of the projected image. For larger build areas, resolution may decrease because the same number of pixels must cover a broader surface.
SLA
Stereolithography (SLA) is the original 3D printing technology, introduced in the 1980s. It uses a UV laser to selectively cure liquid resin into solid layers. The laser traces the design of each layer directly onto the resin surface, solidifying the material in precise locations.
SLA is renowned for its exceptional precision, achieving resolutions as fine as 25 microns. This high accuracy makes it ideal for applications requiring intricate details, such as jewellery, dental moulds, and medical devices. The smooth surface finish of SLA-printed parts also reduces the need for extensive post-processing.
Vat Photopolymerization materials
Vat photopolymerisation materials differ depending on the process. Each resin type is formulated to optimise performance for its respective printing process.
SLA supports a broad range of resins, including standard resins for general prototyping, tough resins for impact resistance, flexible resins for elastomeric properties, high-temperature resins for heat resistance, and biocompatible resins for medical and dental applications.
DLP, known for its speed and detail, works with standard, rigid, transparent, and castable resins, designed to take advantage of its rapid curing capabilities.
LCD technology is compatible with cost-effective resins such as standard and water-washable types, along with more specialised options like tough or flexible resins tailored for small-scale and hobbyist applications.
VAT photopolymerization applications
Vat photopolymerisation has a wide range of applications due to its precision and versatility. In the medical and dental fields, it is used to create surgical instruments, dental aligners, and prosthetics with exceptional accuracy and biocompatible materials. The jewellery industry benefits from its ability to produce detailed and intricate moulds for casting. Engineers and product designers use the technology for rapid prototyping, functional testing, and creating small-scale production parts.
In addition to these, Vat photopolymerisation is often employed in the automotive and aerospace sectors for creating highly detailed, lightweight components. It is also widely used in education and research for producing complex models and testing innovative materials. The ability to work with a variety of resins tailored for different properties makes it suitable for both decorative and functional applications across diverse industries.
FAQ
Can I print with multiple colors or materials using Vat photopolymerization?
Advanced Vat photopolymerization printers can print in multiple colors or materials by swapping resins during the print process. Most consumer-grade printers are limited to a single resin at a time. For multi-material prints, users may need to manually switch resins or post-process prints to add color or texture
Is Vat photopolymerization suitable for prototyping?
Yes, vat photopolymerization is an excellent choice for prototyping due to its high level of detail and the ability to produce complex geometries quickly. It is commonly used in industries like automotive, aerospace, and healthcare to create functional prototypes for testing and validation.
Are Vat photopolymerization prints durable?
The durability of prints made with Vat photopolymerization depends on the type of resin used. Standard resins are typically more brittle than other materials like PLA or ABS. However, there are ways to reduce brittleness of 3D resin prints, adding higher durability, flexibility, or impact resistance.
Can Vat photopolymerization be used for large-scale prints?
While Vat photopolymerization is great for high-detail prints, it is typically not the best method for large-scale objects due to size limitations of the print bed and slower print speeds. Large prints may require multiple pieces to be printed and then assembled.
What types of products are best suited for Vat photopolymerization?
Vat photopolymerization is ideal for creating highly detailed, small to medium-sized objects, including jewelry, dental models, orthodontic devices, prototypes and concept models as well as custom parts for engineering and design, just to name a few.
Your personal contact
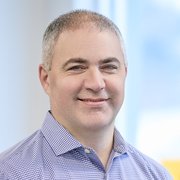
Christopher Cocklan
3D Printing Business Development Manager EnergyCuring
RAHN USA Corp.